WMCentral – Warehouse Management System
WMCentral Enterprise Suite is an end-to-end enterprise-grade Warehouse Management System that can also integrate with the Automated Storage and Retrieval System.
This suite covers all warehousing activities such as receiving, put-away, storage, inventory management, supply, replenishment, kitting, order fulfillment, picking, checking, packing, and dispatch, by keeping track of each of the activities leveraging advanced data capture using Barcode labelling/RFID tagging and related technologies.
It provides visibility of inventory through the entire life cycle of goods getting processed through the Warehouse Management System, right from the time it enters the warehouse until it leaves the facility.
WMCentral not only automates warehouse operations, but it also supports in significantly reducing the operating cost by shortening order-fulfillment cycles and maximizing efficiency. It boosts productivity by using Task Interleaving features for high throughput, reduces inventory costs by implementing MOQ and automated replenishment to minimize holding excess stock, and improves inventory accuracy.
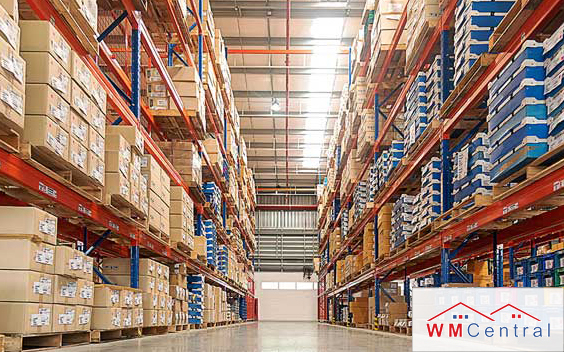
Features
WMCentral allows you to efficiently and effectively manage your Warehouse Operations with the below-streamlined set of integrated features.
Dock Management
Storage Locations Management
Receiving
Cross-docking
Supply for Pre-packing and Packing
Packing
Order Processing
Inventory Management
Task Interleaving
Replenishment
Invoice & Invoice Reversal
Inventory Cycle Count
Equipment Monitoring and Management
Special Features:
Integrates with all components of Automated Systems including:
Technical Features